Application of thermal transfer printing on perfume glass bottles | GP Bottles OEM ODM Manufacturing
Application of thermal transfer printing on perfume glass bottles | GP Bottles OEM ODM Manufacturing
The heat transfer film is a technique that prints patterns and glue on a heat-resistant film, and adheres the pattern (ink layer) and glue layer to the glass bottle by heating and pressure. This process is mostly used on plastic and paper, and less used on glass-wrapped bottles.
Process flow: 1. Color draft; 2. Film printing; 3. Thermal transfer; 4. Baking.
The heat transfer film is generally divided into five layers, the surface PET film layer is used as the carrier, and the separation layer plays a role of being heated and suitable for falling off. The protective layer plays the role of protecting the ink layer, the ink layer is pattern printing, and the adhesive layer is the adhesion layer.
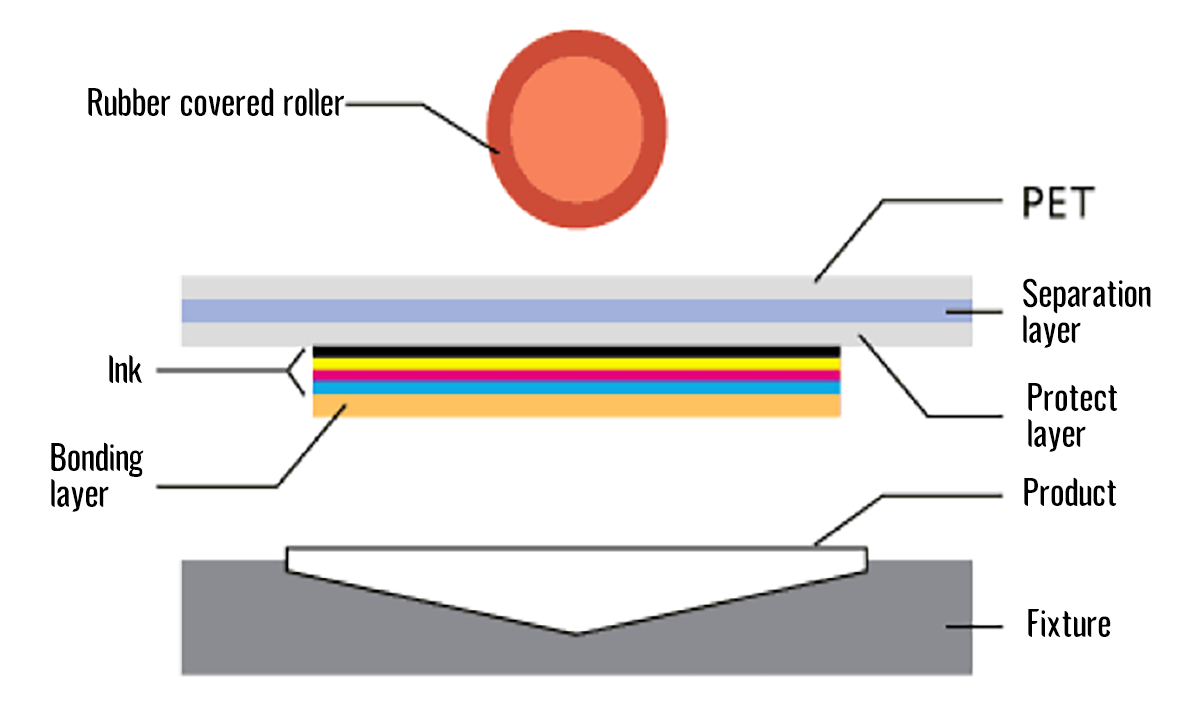
Since the multi-color pattern can be formed into a picture at one time in the film printing stage, the existing pattern can be transferred to the glass bottle at one time during the transfer operation on the glass bottle. Compared with the cumbersome set of multi-color silk screen printing, it can greatly shorten the printing work and reduce the material loss caused by printing errors. At present, the labor cost is constantly rising, and the customers' requirements for accurate and high-quality set-ups, so in the multi-color manuscript, the advantage of thermal transfer is very obvious.
In addition, in the film printing stage, CMYK printing is routinely used, and spot color printing can also be performed according to customer requirements. The effect of thermal transfer is more realistic, the color reproduction is high, and gradual color can be achieved. Due to the thermal baking of the image, the color of the finished image will be stronger than that of the water transfer, and it will not fade easily. It has good properties such as corrosion resistance, aging resistance, abrasion resistance, and high temperature resistance.
In the processing of glass bottles, compared with water transfer printing and silk screen printing, thermal transfer has obvious advantages.
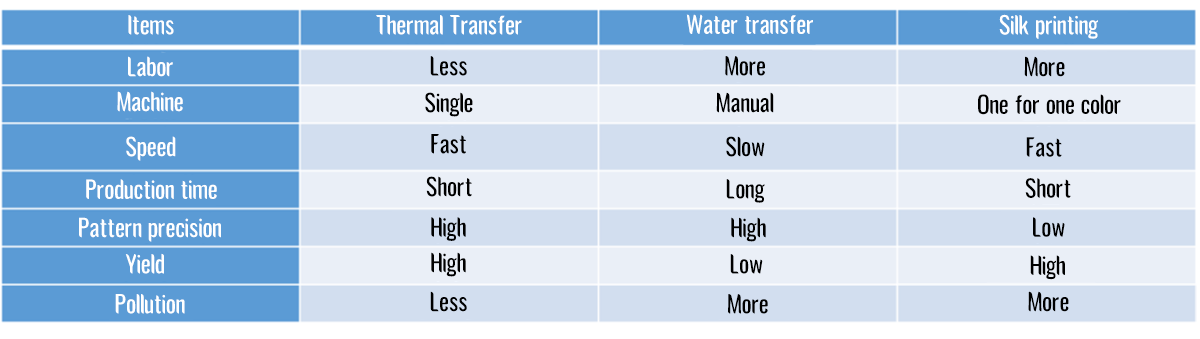
In general, compared with the traditional water transfer and silk screen printing, the advantages of thermal transfer are: less manpower consumption, high degree of automation, fast, accurate color registration, high yield, and less environmental pollution.
However, the disadvantage of thermal transfer is that it requires a higher degree of regularity of the substrate, and it needs to work in a more regular position. The processing of square and cylindrical bottles is very advantageous. The special-shaped bottle needs to be analyzed according to the entity to confirm the processing position.
In the development of thermal transfer, in addition to ordinary toner inks, many new types of pearlescent ink film and mirror ink thermal transfer film, and thermal transfer film with bronzing have also been developed. Looking to the future, the use of heat transfer printing on glass bottles will be more widespread.