Plastic perfume cap injection molding process | GP Perfume Bottles OEM ODM Manufacturing
Plastic perfume cap injection molding process | GP Perfume Bottles OEM ODM Manufacturing
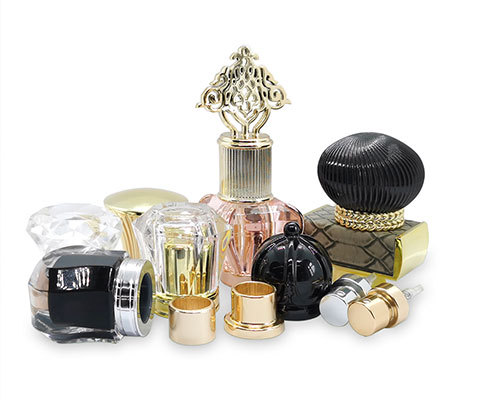
1. Filling stage
Filling is the first step in the entire injection cycle process. The time starts from when the mold is closed and the injection is started until the mold cavity is filled to about 95%. In theory, the shorter the filling time, the higher the molding efficiency, but in practice, the molding time or injection speed is restricted by many conditions.
High-speed filling: The shear rate is high during high-speed filling, and the viscosity of the plastic decreases due to the effect of shear thinning, which reduces the overall flow resistance; the local viscous heating effect will also make the thickness of the solidified layer thinner. Therefore, in the flow control stage, the filling behavior often depends on the volume to be filled. That is, in the flow control stage, due to the high-speed filling, the shear thinning effect of the melt is often great, and the cooling effect of the thin wall is not obvious, so the effect of the speed prevails. l
Low-speed filling: When the low-speed filling is controlled by heat conduction, the shear rate is lower, the local viscosity is higher, and the flow resistance is larger. Due to the slower replenishment rate and slower flow of the hot plastic, the heat conduction effect is more obvious, and the heat is quickly taken away by the cold mold wall. Coupled with a smaller amount of viscous heating, the thickness of the cured layer is thicker, which further increases the flow resistance at the thinner part of the wall. l
Generally speaking, the strength of the weld line produced in the high temperature zone is better, because the polymer chains are more mobile and can penetrate each other under high temperature conditions. In addition, the temperature of the two melts in the high temperature zone is closer. The thermal properties are almost the same, which increases the strength of the welding area; on the contrary, in the low temperature area, the welding strength is poor.
Second, the pressure holding stage
The function of the holding pressure stage is to continuously apply pressure, compact the melt, and increase the density (densification) of the plastic to compensate for the shrinkage behavior of the plastic. During the pressure holding process, the back pressure is relatively high because the mold cavity has been filled with plastic. In the process of maintaining pressure and compaction, the screw of the injection molding machine can only move forward slowly, and the flow speed of the plastic is relatively slow. The flow at this time is called the pressure maintaining flow. In the pressure holding stage, the plastic is cooled and solidified by the mold wall faster, and the melt viscosity increases quickly, so the resistance in the mold cavity is very large. In the later stage of pressure holding, the material density continues to increase, and the plastic parts are gradually formed. The pressure holding stage should continue until the gate is cured and sealed. At this time, the cavity pressure in the pressure holding stage reaches the highest value.
In the pressure-holding stage, the plastic exhibits partial compressibility due to the relatively high pressure. In the higher pressure area, the plastic is denser and the density is higher; in the lower pressure area, the plastic is looser and the density is lower, so the density distribution changes with position and time. In the process of holding pressure, the plastic flow rate is extremely low, and the flow no longer plays a leading role; pressure is the main factor that affects the process of holding pressure.
Three, cooling phase
In the injection molding mold, the design of the cooling system is very important. This is because the molded plastic product can only be cooled and solidified to a certain rigidity, and then the plastic product can be prevented from being deformed due to external force after being demolded. Since the cooling time accounts for about 70% to 80% of the entire molding cycle, a well-designed cooling system can greatly shorten the molding time, improve injection molding productivity, and reduce costs. An improperly designed cooling system will lengthen the molding time and increase costs; uneven cooling will further cause warpage and deformation of plastic products.
Fourth, demoulding stage
Demoulding is the last link in an injection molding cycle. Although the product has been cold-formed, demolding still has a very important impact on the quality of the product. Improper demolding method may cause uneven force on the product during demolding, and product deformation during ejection. There are two main ways of demolding: ejector rod demoulding and stripping board demolding. When designing the mold, choose the appropriate demoulding method according to the structural characteristics of the product to ensure the quality of the product.